The switched reluctance motor – SRM – is regarded as the most intelligent solution for magnetless electric motor drive. Researchers are working hard to remove all barriers to commercialising the technology because it can provide better efficiency and performance for a wide range of applications. Although SRM is not a new motor, technological advancements have made it possible to reconsider this cost-effective alternative for industrial drives.
To identify research gaps, it is necessary to examine the existing issues with commercialising the SR Motor.
Issues with Switched Reluctance Motor Drive
- SRM always required a power electronics converter and controller which resulted in additional cost to the system. Thus, competing conventional Induction Motor for the fixed speed applications becomes tough for the SRM.
- SRM always requires a rotor position sensing system which results in additional cost and complexity. It also affects the reliability of the system depending upon the type of the rotor position sensing system.
- Torque of the SRM depends on phase currents and rotor position, which when operated with step-wise currents result in significant torque ripple. Thus, torque ripple minimization schemes need to be incorporated with conventional control schemes.
- Due to SRM salient pole structure, its airgap does not remain constant like other motors and it varies with rotation. This unequal airgap results in unbalanced magnetic pull on the rotor pole which results in torque ripple and acoustic noise. Thus, the torque ripple and acoustic noise both are high in the SRM compared to other motors. Torque of the SRM depends on phase currents and rotor position. Thus, the implementation of the torque ripple minimization schemes becomes more complex and computation intensive. Thus, the requirement of smooth torque control and low noise performance may add extra cost to the SRM drive.

Latest Research Trends in Switched Reluctance Motor Drive
The researchers around the world are trying to solve the issues of the SRM to provide feasible solutions with reasonable cost and performance.
The interest for the SRM is increasing exponentially amongst researchers and scientists around the world. Figure shows year by year growth in the numbers of articles published on SRM in the IEEE journals and conferences.
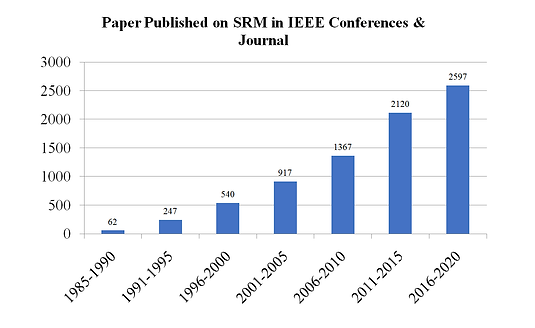
New research scholars can work on one of the following topics depending upon the selected application or individual’s interest.
1 Motor Design:
Designing a motor is a most important and essential task to start a manufacturing unit for any motor industry. The SRM offers a wide range of motor topology as well as converter topology. Thus, it is important to design an SRM to meet requirements and challenges of an application. To achieve a speed-torque performance for an application with compact size and higher efficiency is a prime goal of the motor design. In addition to that, reducing acoustic noise and torque ripple at design level is the latest interest of researchers.
Researchers use high-end software like Ansys Maxwell to design and to analyse the performance of the SRM. Thus, working on the design goal of an SRM needs practice on such software. One dimension is finalized, there should also be an industrial support to manufacture the prototype of a designed SRM. So, most people working on the design goal belong to the R&D department of an industry rather than the academic research scholar.
2 Converter Topology:
The main objective of the research in the field of converter topology is to improve the efficiency of the converter and reduce the cost of the converter. It includes design and development of new converter topologies and switching schemes. Reducing the number of switching devices per phase is the most common way of improving efficiency and cost. However, selecting a switching frequency also plays an important role to balance the performance and efficiency. Lower switching frequency reduces the switching losses but it may increase the torque ripple.
Thus, to work on converter topology is about analysing placements of power electronics switches and its operation. However, numbers of converter topologies for the SRM have already been published in the past literature including one switch per phase type converter. Thus, most researchers prefer to just select a power electronics converter topology suitable for the application and to work with the controller design instead of converter topology. Thus, there are very limited scopes to work in the field of converter topology of the SRM.
3 Controller Design:
We have already discussed in the previous chapter that the design of a closed-loop controller is quite a challenging task for the SRM drive. To select a control scheme and to design a closed loop control system to meet the requirement of an application is an important task. Dependency of the torque developed on the rotor angle makes it more complex compared to other motors. Finding an optimum commutation angle and to achieve a minimum torque ripple are the main goals of most controller design applications. The sophisticated techniques like DTC, sliding mode control and even an AI based control & optimization techniques have been used to design the controller of the SRM.
Thus, there is a huge scope of work in the field of controller design of the SRM. Main objectives of the controller design are to improve the torque ripple, acoustic noise and torque-speed characteristics of the motor.
4 Sensorless Operation:
Eliminating a requirement of the mechanical position sensor can reduce the cost and size of the SRM drive. It may also improve the reliability of the system. Many methods for estimating rotor position have already been published in the literature to enable sensorless operation of SRMs. There is still a lot more to explore and to contribute in the field of rotor position estimation of the SRM.
5 Mathematical Modelling:
Mathematical model of the motor is required to test the converter and control strategy. Mathematical model represents a motor in the form of a mathematical equation. To derive the mathematical model of an SRM is a little bit complex due to its nonlinear magnetic characteristics. Several methods have been proposed in previous literature to develop the mathematical model of the SRM. Most researchers use the built-in SRM model available in the MATLAB library to analyse the performance of their control strategy and converter. However, several researchers are also working on the development of a new and improved mathematical model of the SRM.
The study of mathematical modelling of an SRM is a very important component for any researcher studying SRM, regardless of their area of interest. This is because it also provides an understanding of the limitations of the SRM model. It is important as this model is use to validate a control strategy or the performance of the converter.
6 Investigation and Analysis:
Although the SRM is most suitable for the electric vehicle applications, researchers are exploring and validating new applications of the SRM drive. SRM also has proven good results for various applications like pumps, blowers, power steering and high-speed aerospace applications. Thus, investigating the performance of the SRM drive for a particular application is also a topic of interest for many researchers.
It also includes investigation of torque ripple or noise for different applications, different motors, different switching frequency and or different control techniques. Investigation and analysis of different sensorless control techniques is also latest interest of industries. It includes comparative analysis and suggestion to help selecting best sensorless technique for a particular application.
So, if you are interested in starting your research career in the field of SRM drive, then you can select the one from the above.
If you are new to the switched reluctance motor and want to explore more, then you can checkout self-paced course “Fundamentals of Switched Reluctance Motor and Drive“.
If you already completed this course or know the basic about SRM, then you can checkout the course “Modelling and Simulation of Switched Reluctance Motor Drive“.
Here are some more articles on SRM you might like to read.
- Rebirth of an oldest Electric Motor: Switched Reluctance Motor
- What is the major difference between the BLDC and SRM motor? Which is better? Why?
Thank you